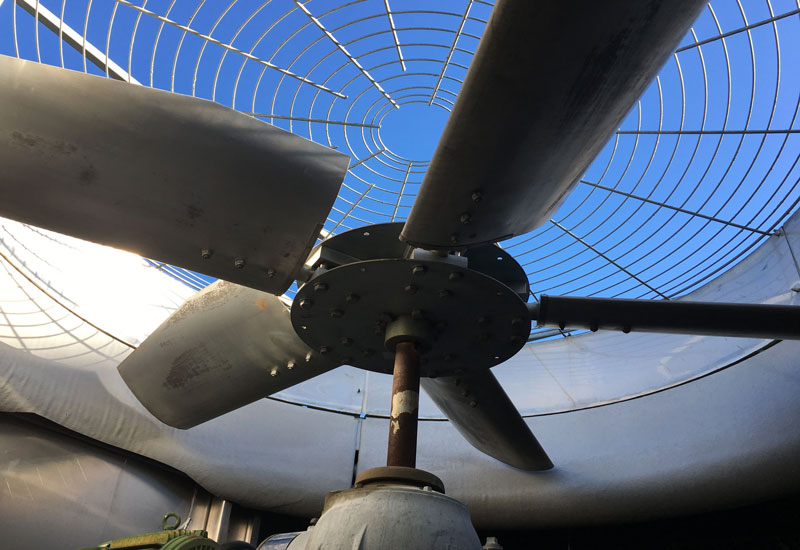
In the modern world, many industries are actively solving the problem of extending the service life of industrial equipment and reducing operating costs. A sizeable portion of an organization’s spending goes into operating costs for the upkeep of industrial equipment, which are occasionally equal to profit. When it comes to vibration analysis services Denver, rotating machines—such as electric motors, compressors, turbines, generators, drives, pumps, etc.—are the most significant and susceptible industrial components.
Currently, there are three main strategies for equipment maintenance:
· Reactive maintenance, which consists of uncontrolled operation of equipment until failure. This method brings significant losses due to downtime required to eliminate unexpected failures. This method is gradually being displaced from the production sphere and is used mainly for cheap auxiliary equipment;
· Maintenance based on scheduled preventive maintenance. This type of repair involves carrying out preventive work strictly according to a schedule. This method is the most common and is the basic one for most enterprises. Unfortunately, scheduled preventive maintenance does not allow for a significant reduction in maintenance costs, since at least 50% of all scheduled maintenance is performed without any actual need;
· Maintenance based on the assessment of the actual condition of the equipment. This method consists of monitoring the technical condition of the equipment using modern means of technical diagnostics and carrying out repair work only when it is really necessary. As a result of continuous diagnostics of the equipment in operation, it is possible to reduce the volume of work due to the systematic suppression of the causes of defects;
The use of vibration analysis services allows for obtaining significant economic benefits that can be achieved due to the possibility of:
- Avoid accidents
- Virtually eliminate unexpected stops and unplanned equipment downtime.
- Analysis of vibration diagnostic data allows vibration analysis companies to draw up a clear schedule of maintenance and plan preventive or major repairs when the technical condition of the equipment requires it.
- Significantly reduce and efficiently use spare parts inventory.
- Identify faults at an early stage. Even minor faults that cannot be identified by analyzing the overall vibration level will be recorded promptly, and in the future, it will be possible to monitor the dynamics of their development and plan the date required for elimination.
- Accurate diagnostics prevent overstocking and understocking of spare parts.
- Vibration analysis provides precise fault identification, leading to more accurate and effective repairs.
- Data-driven insights allow for better planning of production schedules around maintenance activities.
- Vibration analysis aids in predicting future equipment issues based on historical data trends.
- By reducing unexpected breakdowns, workers can focus on their tasks without interruption.
- Regular monitoring and maintenance help meet safety regulations and standards.
Significant global experience in the application of condition-based maintenance allows :
Reduction of maintenance costs: Vibration analysis companies significantly lower maintenance costs by transitioning from routine scheduled maintenance to condition-based maintenance. By using vibration analysis services to monitor equipment health in real time, companies only perform maintenance when necessary. This targeted approach minimizes unnecessary work and reduces labor and material expenses, leading to substantial cost savings.
Reduction in the number of services: Vibration analysis companies help reduce the number of maintenance services needed by enabling precise diagnostics of equipment conditions. By detecting and addressing issues early, these companies prevent the escalation of minor faults into major problems, thereby reducing the frequency of maintenance interventions and extending the time between service requirements.
Reduction in failure rates in the initial years of operation: Utilizing the expertise of vibration analysis companies near me results in lower failure rates during the initial operational years. Early detection and remediation of potential issues through vibration monitoring help maintain optimal performance and prevent premature equipment failures, ensuring a more reliable and efficient operation from the start.
In summary,
Efficient maintenance techniques are essential in today’s industrial environment to maximize equipment longevity and save expenses. Vibration analysis firms provide an advanced strategy by emphasizing condition-based maintenance as opposed to reactive or planned preventive maintenance. This method improves equipment dependability, minimizes operating expenses, cuts down on needless maintenance, and aids in early defect discovery. Vibration analysis may help companies save money by optimizing resource use, minimizing downtime, and increasing operational effectiveness. Vibration analysis thus stands out as a vital instrument for bringing maintenance procedures up to date and attaining long-term sustainability in industrial operations.