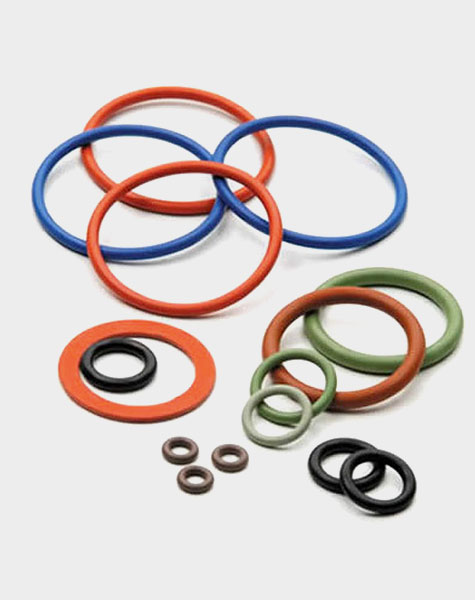
Even though O rings are all around us in the industry, many people may still be unsure of what they are. And what purpose do O rings serve? How do they differ from other kinds of seals? O rings come in a wide variety and serve as a seal to safeguard the machinery and guarantee optimal operation. They are available in various sizes and can be created using a range of materials and techniques, such as extrusion or molding. Nonetheless, they all achieve the same main objective. O Ring Seals serve the purpose of sealing the joint between two items to prevent the passage of liquid, gas, or air. Let’s take a closer look at what o-rings do and some of their most common applications.
What are the applications of O-ring seals?
O ring seals are widely used for various applications in different industries:
O-rings for sealing at high temperatures
As the name suggests, high-temperature sealing o-rings are made to withstand extremely high or low temperatures while still maintaining a strong seal between two surfaces or components. This makes them perfect for demanding industries and situations like as oil and gas refineries, chemical processing, and any other scenario that necessitates a high-temperature seal, such as performance transportation applications like turbo engines and aerospace engineering.
There are several popular high-temperature o-ring materials, including nitrile, hydrogenated nitrile, silicone rubber, polyacrylate, and more. Securing the best decision in any particular circumstance will typically be a balancing act between the required operating temperature and the most cost-effective material option at that performance level.
O Ring Seals for high-pressure
These ring seals are widely used O-rings used in high-pressure sealing. High-pressure resistance is a typical need for industrial o-rings as is consistent performance in high-temperature and dynamic situations. For a high-pressure seal to function optimally o-ring design and fabrication rely on selecting appropriate materials for improved performance under specified conditions.
O-rings work on the idea that even pressure applied to the (more or less incompressible) o-ring material results in predictable deformation patterns around the gasket’s perimeter in its groove. This means that an O-ring’s contacting surfaces are subjected to a rather homogenous mechanical stress. Even under high pressure, leaks are nearly impossible if the internal pressure from the fluids being confined remains below the contact stress rating of a specific O-ring.
O-ring seals for engines
An engine o-ring, particularly one used in high-performance or turbo engines, is a good example of a device that must be tough in design and material composition to withstand a variety of demanding temperature, pressure, and chemical compatibility criteria.
Many basic rubbers and polymers are not compatible with oils, fuels or solvent-based chemicals. For use in an engine, an oil o-ring must be made specifically from compatible hybrid materials that allow it to maintain critical o-ring properties (flexibility, incompressibility) while providing more benefits than a standard elastomer.
Plumbers use O ring seals
Plumbing o-ring options are plentiful, given the variety of materials, sizes, and gauges available for use in ducting and pipework applications, as well as to form strong watertight seals around taps and other connections. Choosing the best product for the job requires determining the proper size and shape for the specific role you intend to fill.
Seals made of food-grade O-rings
Food-grade o-rings have been created to more stringent material composition criteria. They should have been legally designated as ‘food safe’ for use in the production and preparation of meals, beverages, and dining items.
O Ring Seals for CO2
Carbon dioxide is a common concern for many types of o-rings because softer materials absorb the gas and swell with time. This can result in an unsatisfactory seal in the short term, and the CO2 will eventually cause the o-ring to break down from within.
Polyurethane, PTFE, nitrile, and fluoroelastomers are popular alternatives for usage in applications where the o-ring will come into extended contact with CO2. However, the optimal option will always be determined by other environmental or application considerations.
O-ring seals for aerospace
Aircraft o-rings and aerospace o-rings must be extremely chemically resistant and able to work throughout a wide temperature and pressure range to maintain an aircraft craft’s powertrain running cleanly, efficiently, and smoothly. Fuel cap gaskets, fuel system o-rings, and valve cover seals are among the most common applications.
Nitriles, ethylene propylene, fluorosilicones, and other elastomers are commonly used in aeronautical applications. Because most aircraft engines and systems employ a variety of o-ring sizes and gauges, bulk orders of multi-size o-ring kits account for the majority of aerospace and aeronautics sales.
Final Words
Perfluoroelastomer FFKM O-rings are widely utilized in several sectors for sealing purposes. If you need a sealing solution that can withstand harsh conditions, FFKM O Ring Seals are the best option.
Horiaki India Private Limited is the leading manufacturer and supplier of these O-rings with customizable requirements. As one of India’s top manufacturers of Perfluoroelastomer FFKM O-rings, we use high-quality raw materials and thoroughly test them before delivering them to customers.
Frequently Asked Questions
What are the purpose and benefits of using O Ring Seals?
These are very easy to use, with no spreading or retightening required. Tightening produces no critical torque, making structural damage improbable. O-rings typically occupy little space and are low in weight. In many circumstances, O-rings can be reused, giving them an advantage over non-elastic flat seals and crush-type gaskets.
What is the distinction between O-rings and seals?
A seal ring is a solid metal ring used to provide a static seal between two surfaces, whereas an O-ring is a flexible, circular ring made of rubber or elastomer that is used for dynamic sealing in a variety of mechanical applications.
What is the most significant disadvantage of an O ring?
They can be employed in both static and dynamic applications, however high-speed movement can diminish their usefulness. This is because the material must bounce back after being compressed by the movement, and in instances involving fast-moving machinery, an O ring may not restore its shape quickly enough to be 100% effective. They are best suited for slower-moving dynamic applications such as shafts, spindles, and rotary transmission lead-throughs. They can handle pivots, rotation, and spiral movement.