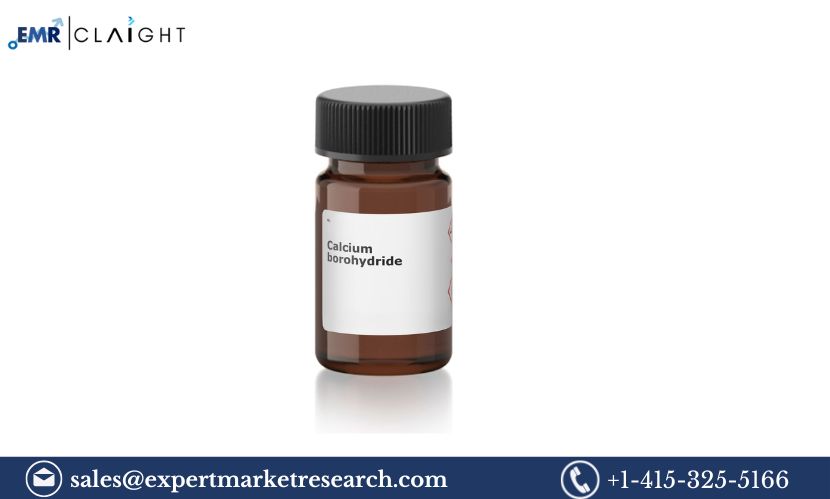
Introduction
Calcium Borohydride (Ca(BH₄)₂) is an important chemical compound primarily used in applications such as hydrogen storage, fuel cells, and chemical reduction processes. Due to its high hydrogen content, it has attracted attention for its potential in energy storage systems and sustainable energy solutions. The Calcium Borohydride Manufacturing Plant Project Report offers a comprehensive overview of the steps involved in setting up a manufacturing plant for Calcium Borohydride. This includes information on raw materials, production processes, required equipment, market demand, and financial viability.
Key Considerations for Setting Up a Calcium Borohydride Manufacturing Plant
1. Raw Materials
The production of calcium borohydride requires a few key raw materials:
- Calcium Hydride (CaH₂): This is one of the primary starting materials for the synthesis of calcium borohydride. It is typically used for hydrogenation reactions due to its strong reducing properties.
- Borohydride Source: The boron source, usually sodium borohydride (NaBH₄), is mixed with calcium hydride to form calcium borohydride. The reaction occurs under controlled conditions to ensure the correct product is obtained.
- Solvents and Stabilizers: Depending on the specific production method, solvents like tetrahydrofuran (THF) or other non-aqueous solvents might be used to maintain the stability of the compounds during synthesis.
The availability, quality, and cost of these raw materials will influence the overall cost-effectiveness and feasibility of setting up a manufacturing plant.
Get a Free Sample Report with Table of Contents@
2. Manufacturing Process
The manufacturing process of calcium borohydride generally involves the reaction between calcium hydride and a borohydride source. A common method is the reaction of calcium hydride with sodium borohydride in a solvent like tetrahydrofuran (THF) or other appropriate media. The process typically includes the following stages:
- Synthesis: The primary synthesis step involves mixing calcium hydride with sodium borohydride under controlled conditions. This is typically carried out in a sealed reactor where temperature, pressure, and reaction time are carefully monitored.
- Hydrogenation: In some methods, hydrogen gas is introduced into the reaction to promote the formation of calcium borohydride from the calcium hydride and sodium borohydride.
- Purification: After the synthesis, the resulting calcium borohydride is purified to remove any impurities or unreacted starting materials. This step is critical to ensure that the final product is of high purity, which is crucial for its use in sensitive applications such as hydrogen storage.
- Drying and Packaging: The final product is dried to remove any solvent residues and packaged in moisture-resistant containers to prevent degradation. Calcium borohydride is sensitive to moisture and can decompose if exposed to water or humidity.
This manufacturing process involves handling reactive chemicals, so safety protocols are essential to prevent accidents and ensure the smooth operation of the plant.
3. Required Equipment and Machinery
To set up a calcium borohydride manufacturing plant, a variety of specialized equipment is necessary:
- Reactor Vessel: The reactor is the core of the manufacturing process, where the chemical reaction between calcium hydride and sodium borohydride takes place. It must be made of materials that can withstand high temperatures and pressures, such as stainless steel or alloy materials.
- Hydrogenation Unit: If hydrogenation is part of the process, a hydrogenation unit is required to introduce and control the flow of hydrogen gas into the reactor.
- Distillation and Purification Units: These are used to purify the calcium borohydride after the synthesis process. Distillation or filtration systems are employed to remove unwanted impurities and solvents.
- Drying Systems: Given the hygroscopic nature of calcium borohydride, drying systems are needed to remove any residual solvents or moisture after the product has been synthesized.
- Packaging Machines: The final product must be packaged in airtight, moisture-resistant containers. Packaging machines will be required to fill, seal, and label containers for transport and sale.
Investing in high-quality, durable machinery is essential to ensure consistent production quality, prevent downtime, and reduce maintenance costs.
4. Plant Layout and Infrastructure
The layout of the Calcium Borohydride Manufacturing Plant should be designed with safety, efficiency, and scalability in mind. Some key considerations include:
- Raw Material Storage: Adequate space is required to store the raw materials, such as calcium hydride and sodium borohydride, as well as solvents. This area should be well-ventilated and separated from other parts of the plant to prevent contamination or accidents.
- Production Area: The production area should be spacious enough to house the reactor, hydrogenation units, purification systems, and drying equipment. The plant should also have a system for handling and transporting materials safely between different stages of production.
- Quality Control Lab: A dedicated space for testing the purity and quality of the calcium borohydride should be part of the plant’s infrastructure. The lab should be equipped with instruments for analyzing the chemical composition and ensuring that the product meets required standards.
- Storage and Packaging: After production, the calcium borohydride should be stored in a controlled environment. A separate packaging area should be set up for sealing the final product into appropriate containers.
- Safety Systems: Given the reactive nature of some of the chemicals used in the production process, safety measures such as fire extinguishers, explosion-proof equipment, and proper ventilation systems are critical.
5. Market Demand and Applications
Calcium borohydride’s most prominent application is in hydrogen storage. Its ability to release hydrogen when exposed to water makes it a potential candidate for use in fuel cells and hydrogen-powered vehicles. Other uses include:
- Chemical Reduction: In organic chemistry, calcium borohydride is used as a reducing agent in reactions such as the reduction of aldehydes and ketones to alcohols.
- Energy Storage: The growing demand for alternative energy sources has led to the increased interest in calcium borohydride as an energy storage solution.
- Metal Hydride Systems: In addition to hydrogen storage, calcium borohydride can be used in various metal hydride systems for energy storage and other applications.
With the global focus on sustainability and renewable energy, the demand for products like calcium borohydride is expected to increase in the coming years. This provides an excellent market opportunity for manufacturers in the specialty chemicals sector.
6. Financial Feasibility and Investment
The setup costs for a Calcium Borohydride Manufacturing Plant can be substantial, with significant investments required for land acquisition, machinery, and infrastructure. However, the plant’s profitability will largely depend on:
- Production Capacity: A higher production capacity typically translates to economies of scale, reducing the per-unit cost of production and increasing profitability.
- Raw Material Costs: The price of raw materials, particularly calcium hydride and sodium borohydride, will impact production costs. Negotiating favorable prices with suppliers can help manage costs.
- Market Prices and Demand: The price at which calcium borohydride can be sold, along with the demand for the product in various industries, will determine the revenue generated from the plant.
- Operational Efficiency: Streamlining operations, minimizing waste, and maximizing production uptime will help in maintaining profitability.
Financial projections, including a break-even analysis and ROI, will help in determining the feasibility of the project.
FAQs
1. What are the primary uses of calcium borohydride?
Calcium borohydride is primarily used for hydrogen storage, fuel cells, and chemical reduction reactions. It also finds applications in energy storage systems.
2. What raw materials are needed to produce calcium borohydride?
The key raw materials are calcium hydride (CaH₂) and sodium borohydride (NaBH₄), along with solvents like tetrahydrofuran (THF) for the synthesis process.
3. What equipment is required for manufacturing calcium borohydride?
Key equipment includes reactors, hydrogenation units, purification systems, drying equipment, and packaging machines.
4. What safety considerations are involved in calcium borohydride manufacturing?
Given the reactive nature of the chemicals, safety protocols such as ventilation systems, explosion-proof equipment, and fire safety measures are essential.
5. What is the market demand for calcium borohydride?
The growing demand for hydrogen storage solutions and renewable energy applications makes calcium borohydride increasingly valuable in the global market.
Media Contact:
Company Name: Claight Corporation
Contact Person: Lewis Fernandas, Corporate Sales Specialist — U.S.A.
Email: [email protected]
Toll Free Number: +1–415–325–5166 | +44–702–402–5790
Address: 30 North Gould Street, Sheridan, WY 82801, USA
Website: www.expertmarketresearch.com
Aus Site: https://www.expertmarketresearch.com.au