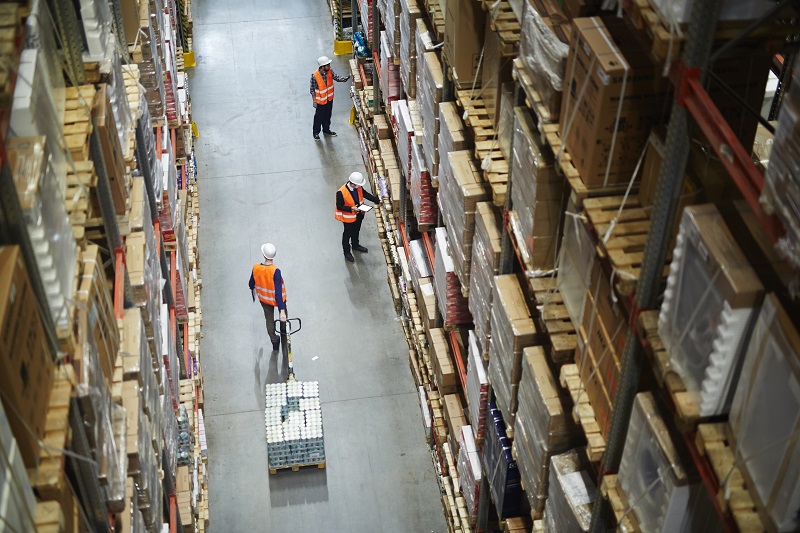
Have you ever walked into a warehouse and thought, “There must be a better way to organise all this space?” Or maybe you’re curious about how to solve warehouse space problems in a way that doesn’t break the bank. These questions often pop up when businesses strive to boost profit while juggling stock, equipment, and day-to-day operations. The good news is that a clever warehouse fitout can make all the difference in your productivity.
Warehouses aren’t just large boxes filled with racks and crates. They act as the backbone of many businesses, especially in Melbourne’s vibrant marketplace. Careful planning—from mapping out floor plans to sorting out post-construction inspections—can help you cut costs, avoid bottlenecks, and deliver products swiftly. Everything from evaluating warehouse shells in Melbourne to using warehouse design software can contribute to a profitable system.
Why A Profitable Warehouse Fitout Matters
Long before you pick up a toolbox or install new racking, it’s vital to understand why a profitable warehouse fitout is so important. Perhaps you want to reduce operational hiccups or you’re looking to make better use of those tight corners. Regardless of your motivation, the right design of warehouse layout not only upgrades day-to-day operations but also sets the foundation for long-term success.
One key point lies in efficient order fulfilment. Picture what happens when stock is buried in the wrong zone. Staff waste precious moments looking for items, and shipping deadlines can slip. A warehouse layout that focuses on minimising travel time enables quick picking, packing, and dispatching. This alone can contribute to a substantial increase in customer satisfaction and, indirectly, a boost in revenue.
Key Considerations Before Designing A Warehouse
Before diving into the design phase, it’s critical to evaluate what you have and what you really need. This can involve not only the physical building but also intangible factors such as workflow, employee safety, and compliance with local regulations.
Evaluating Warehouse Shells In Melbourne
Melbourne is known for its diverse range of industrial real estate. The region’s warehouse shells vary in size, ceiling height, and structural capabilities. When you’re crafting a plan for your warehouse layout, look closely at features like floor load capacity, ventilation, and natural lighting. These details can influence everything from forklift usage to employee productivity.
For instance, if you plan on storing heavy goods, the floor must handle the load. Likewise, older warehouse shells in Melbourne might require additional insulation or comprehensive upgrades to align with modern safety codes. All these elements impact your budget, so do your homework thoroughly.
Warehouse Layout Vs. Warehouse Design: What’s The Difference?
It’s easy to mix up terms like “warehouse layout” and “warehouse design.” Put simply, the layout is the plan of how you position racks, aisles, and operational stations to handle daily tasks. The design, however, can involve more nuanced decisions, like lighting, ventilation, and even aesthetic choices. The layout focuses on floor space efficiency, while design zeroes in on creating a functional, safe, and pleasant environment for staff.
A strong layout might mean shorter routes for forklift operators, while a robust design could include eco-friendly lighting systems that reduce energy costs and foster a better workspace. Both are essential if you wish to build a warehouse that serves you well now and in the years to come.
Budgeting And Costs: Breaking Down Warehouse Construction Cost
Money drives any fitout project, and understanding the real figures behind warehouse construction cost can help you budget more accurately. From raw materials to local labour rates, many factors influence your final expenditure.
Cost To Build Warehouse Space In Australia: An Overview
In Australia, the cost to build warehouse space depends on location, materials, and your desired features. City centres like Melbourne typically have higher construction and labour costs than regional areas. If you’re planning a basic warehouse without climate control or specialised fixtures, the price tag will differ from a more advanced facility designed for temperature-sensitive products.
To avoid surprises, consult local professionals who are seasoned in industrial builds. They can offer realistic quotes, taking into account any site-specific requirements, like soil stability or council regulations. This collaborative approach ensures your commercial vision aligns with practical constraints, saving you time and money in the long run.
Construction And Implementation
After thorough planning, it’s finally time to bring your vision to life. This stage requires consistent coordination among builders, suppliers, and internal stakeholders.
How To Build A Warehouse Step By Step
Learning how to build a warehouse begins with site preparation. From clearing and levelling the land to laying the foundation, each step sets the stage for a stable, long-lasting structure. Next comes erecting the steel framework or tilt-panel walls, depending on your choice of materials. During this phase, conduction of regular quality checks is vital to catch any issues that might escalate later.
Once the main structure is up, it’s time to install amenities such as electricity, plumbing, and fire safety systems. Around this point, you’ll also arrange your racking, mezzanines, or conveyor belts if they’re part of the plan. Finally, test essential features—like security cameras and loading dock rollers—to make sure that everything works before you declare the space operational.
Future-Proofing Your Warehouse
Things change—consumer demands, product lines, and even the kind of technology your employees need to stay efficient. Future-proofing ensures you’ll be ready for those shifts without having to start from scratch.
Scalability: Planning For Growth And Evolving Needs
One element of future-proofing is scalability. If you anticipate higher product turnover or the need to store bigger items, design your warehouse layout with expansion in mind. This might mean leaving space for additional shelving or choosing racking systems that can be extended upward. Don’t forget potential tech advancements, such as automated picking robots, which require specific clearances and pathways.
An agile design also helps you handle shifting consumer preferences. For instance, an e-commerce boom might demand more picking stations to handle smaller, individual orders, whereas a B2B setup might focus on bulk shipping zones. By planning for both scenarios, you’re not locked into one rigid design that can’t adapt.
Conclusion:
Summing up, optimising a warehouse fitout is about more than clever shelves and robust racks. It involves synchronising workflows, anticipating future demands, and making data-driven choices that reduce costs while lifting productivity. Whether you’re evaluating warehouse shells in Melbourne or exploring how to build a warehouse from scratch, each decision can shape your long-term profitability.