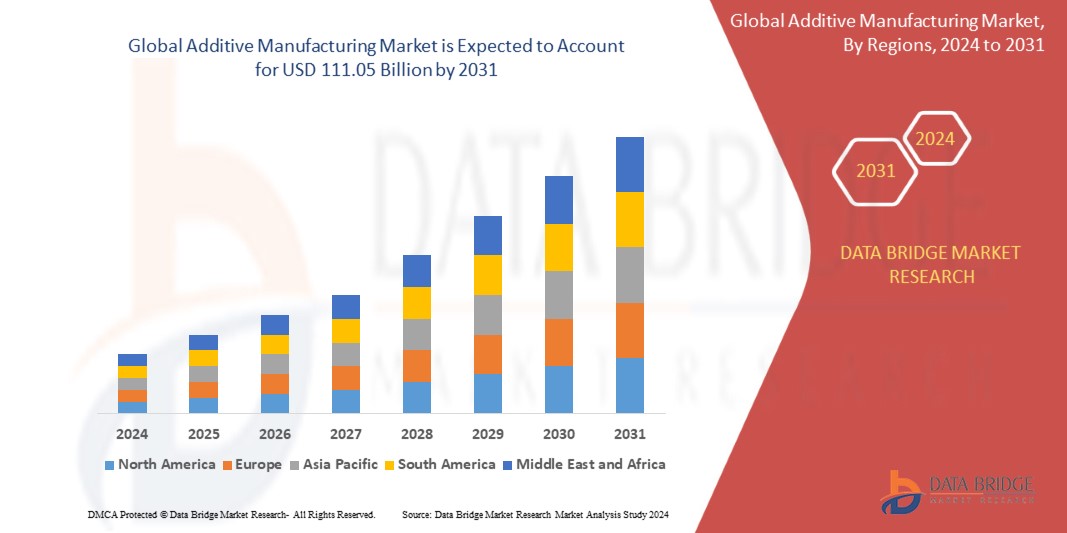
Introduction
The world of manufacturing is undergoing a monumental transformation. Traditional subtractive processes, which rely on removing material from a solid block, are increasingly being complemented—or even replaced—by Additive Manufacturing (AM), commonly known as 3D printing. What was once considered a prototyping technology is now disrupting entire industries, from aerospace and healthcare to automotive and consumer goods.
Additive Manufacturing empowers engineers and designers to rethink how parts are conceived, produced, and delivered. It minimizes waste, reduces lead times, enables unprecedented design freedom, and supports mass customization. In 2023, the global AM market surpassed USD 18 billion, with projections to cross USD 50 billion by 2030.
This guest post delves into the fascinating world of Additive Manufacturing—exploring its principles, processes, applications, industry impact, and future trajectory.
What is Additive Manufacturing?
Additive Manufacturing refers to technologies that build 3D objects by adding material layer by layer based on digital models, typically from CAD files. Unlike subtractive or formative manufacturing, AM enables the direct creation of complex shapes with minimal material waste and fewer process steps.
Key Steps in AM
-
Design: Creation of 3D CAD models
-
Conversion: Slicing the design into layers and converting into machine-readable formats (STL)
-
Material Preparation: Loading material (metal powder, filament, resin, etc.)
-
Printing: Layer-by-layer construction
-
Post-Processing: Curing, surface finishing, heat treatment, or support removal
Major Additive Manufacturing Technologies
1. Fused Deposition Modeling (FDM)
-
Material: Thermoplastic filaments (PLA, ABS, PETG)
-
Popular for: Low-cost prototyping, consumer goods
-
Advantages: Affordable, easy to use
2. Stereolithography (SLA)
-
Material: Photopolymer resin
-
Ideal for: High-resolution models, dental/medical applications
-
Key benefit: Smooth surface finishes
3. Selective Laser Sintering (SLS)
-
Material: Nylon powder or other polymers
-
Common in: Functional prototyping, short-run production
-
Advantage: Strong, functional parts without support structures
4. Digital Light Processing (DLP)
-
Similar to SLA, uses a digital projector for faster prints
-
Applications: Jewelry, dental, small intricate parts
5. Selective Laser Melting (SLM)/Direct Metal Laser Sintering (DMLS)
-
Material: Metal powders (aluminum, titanium, stainless steel)
-
Used in: Aerospace, automotive, medical implants
-
Delivers: High-strength, end-use metal parts
6. Electron Beam Melting (EBM)
-
Material: Metal powders (mainly titanium)
-
Benefits: Ideal for medical and aerospace with superior strength
7. Binder Jetting
-
Binder selectively deposited onto a powder bed
-
Common in: Metal casting patterns, ceramics, sand molds
8. Material Jetting
-
Jetting droplets of material (similar to inkjet printing)
-
Good for: High-quality prototypes with color and smoothness
Key Advantages of Additive Manufacturing
-
Design Freedom
-
Create complex geometries, lattices, and lightweight structures that are impossible with traditional methods.
-
-
Rapid Prototyping
-
Speeds up the development cycle, allowing for faster iterations and time-to-market.
-
-
Mass Customization
-
Each part can be uniquely tailored—ideal for medical devices, dental implants, and consumer products.
-
-
Reduced Waste
-
Material is added only where needed, minimizing scrap and environmental impact.
-
-
Shorter Supply Chains
-
Localized, on-demand production reduces inventory and transportation costs.
-
-
Tool-less Manufacturing
-
Eliminates the need for expensive molds and dies, especially beneficial for small batch production.
-
Industry Applications of Additive Manufacturing
1. Aerospace & Defense
-
Lightweight parts for aircraft and spacecraft
-
Complex fuel nozzles (e.g., GE Aviation’s LEAP engine)
-
Satellite components and rocket engines (e.g., Relativity Space)
2. Automotive
-
Custom fixtures, jigs, and tooling
-
End-use components for luxury and performance vehicles (e.g., Bugatti’s titanium brake calipers)
-
Electric vehicle parts and lightweighting solutions
3. Healthcare & Medical Devices
-
Patient-specific implants (hip, knee, cranial)
-
Dental crowns, bridges, and aligners (e.g., Invisalign)
-
Prosthetics and orthotics with customized fit
-
Bioprinting research (tissue scaffolds, organ regeneration)
4. Consumer Goods
-
Eyewear, fashion accessories, shoes (e.g., Adidas Futurecraft)
-
Personal electronics components
-
Custom phone cases, jewelry, and home decor
5. Industrial & Tooling
-
End-use tools, dies, and molds
-
Spare parts on demand
-
Maintenance, Repair & Operations (MRO)
6. Construction
-
Large-scale 3D printing of buildings and infrastructure
-
Benefits: reduced labor, waste, and faster construction timelines
7. Education & Research
-
Hands-on prototyping in schools and universities
-
Innovation platforms for startups and entrepreneurs
Market Outlook: Global Trends in Additive Manufacturing
Market Size & Forecast
-
The additive manufacturing market size was valued at USD 91.84 billion in 2024 and is projected to reach USD 419.22 billion by 2032, with a CAGR of 20.90% during the forecast period of 2025 to 2032.
Top Regions
-
North America: Dominates due to aerospace and automotive innovation
-
Europe: Strong in industrial and medical AM
-
Asia-Pacific: Rapidly expanding in manufacturing hubs like China, Japan, and South Korea
Growth Drivers
-
Digital transformation in manufacturing (Industry 4.0)
-
Rising demand for sustainable manufacturing
-
Government investments and R&D funding
-
Need for agile, flexible production systems
Challenges and Limitations
-
High Initial Costs
-
Especially in metal AM systems and industrial-scale setups
-
-
Material Limitations
-
Limited range compared to traditional manufacturing (especially in structural metals and composites)
-
-
Post-Processing Requirements
-
Many AM parts require machining, heat treatment, or surface finishing
-
-
Speed and Volume Constraints
-
Slower than injection molding or CNC for high-volume production
-
-
Standardization and Certification
-
Regulatory hurdles in critical sectors like aerospace and healthcare
-
-
Intellectual Property Concerns
-
Risks of 3D file theft or counterfeit production
-
The Rise of Additive Manufacturing in Industry 4.0
AM is a cornerstone of Industry 4.0, synergizing with:
-
AI & Machine Learning: For process monitoring and optimization
-
IoT: Sensor-enabled machines and real-time analytics
-
Cloud Computing: Digital inventory and remote file sharing
-
Digital Twins: Simulating and validating part performance before printing
This convergence is redefining manufacturing as smart, connected, and data-driven.
Sustainability and Additive Manufacturing
Sustainability is a key driver for AM adoption:
-
Less Material Waste: Compared to machining and casting
-
Localized Production: Reduces carbon footprint of transportation
-
Lightweight Designs: Enhances fuel efficiency in transport sectors
-
Recyclable Materials: Many polymers and metals can be reused
Key Players in Additive Manufacturing
Hardware Manufacturers
-
Stratasys: FDM, PolyJet systems
-
3D Systems: SLA, SLS, DMP technologies
-
EOS: Industrial metal and polymer AM
-
HP: Multi Jet Fusion (MJF) for fast polymer printing
-
Desktop Metal: Office-friendly metal AM
-
Markforged: Composite and metal AM
Software Providers
-
Autodesk: Fusion 360, Netfabb
-
Materialise: Magics software suite
-
Siemens NX: CAD, simulation, and manufacturing
-
Ultimaker Cura: Open-source slicing tool
Materials Suppliers
-
BASF Forward AM
-
Evonik
-
Arkema
-
Höganäs
-
Sandvik
Future Outlook: Where is Additive Manufacturing Headed?
1. Mass Production
-
Shift from prototyping to full-scale manufacturing
-
Car parts, consumer electronics, and medical devices at volume
2. New Materials
-
Development of advanced alloys, composites, ceramics, and bio-materials
-
Electrically conductive, antimicrobial, and high-temperature-resistant materials
3. Hybrid Manufacturing
-
Combining additive and subtractive (CNC) processes in one machine
-
More efficient, precise, and versatile production
4. On-Demand Manufacturing Networks
-
Distributed 3D printing farms and service bureaus
-
Enabling faster, localized fulfillment
5. AI-Driven Design & Simulation
-
Generative design for optimized performance and material usage
-
Real-time defect detection and quality control
6. Bioprinting and Organ Regeneration
-
Advancing toward 3D-printed tissues and organs
-
Personalized healthcare with lab-grown implants
Conclusion
Additive Manufacturing is more than just a tool—it’s a paradigm shift. By enabling agility, innovation, and sustainability, AM is poised to redefine how we design, produce, and consume goods. From niche applications to mainstream production, its influence spans industries and continents.
As materials improve, processes mature, and costs decline, the barriers to adoption will continue to fall. Organizations that embrace AM today stand to gain a critical competitive edge in the manufacturing world of tomorrow.