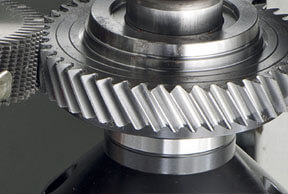
Reliable, quick, and precise production techniques are more important than ever in the precision-driven industrial environment of today. One of the most efficient methods for high- volume manufacture of tiny, complex components is Swiss screw machining. Originally designed in Switzerland to produce watch parts, Swiss-type turning has become a pillar of contemporary production especially in sectors like aerospace, medical, automotive, and electronics.
We will discuss the main benefits of Swiss-type turning in high-volume production in this article, thereby stressing why CNC Swiss machining is the recommended technique for manufacturing intricate, high-precision components on a big scale.
Swiss Screw machining is what?
A Swiss-type lathe—also known as a Swiss automated lathe or Swiss turning center—is used in Swiss screw machining. A Swiss lathe moves the workpiece along the Z-axis using a fixed guide bushing yet unlike other lathes retain the workpiece using a collet. This reduces deflection and vibration by allowing support rather near to the cutting tool.
The initial function of the machine—producing screws and other threaded components—defines the phrase “screw machining.” Modern CNC Swiss machining, however, offers multi-axis capability, live tooling, and high-speed performance for manufacturing components with tight tolerances and intricate geometries, thereby transcending this.
1. Inaccurate Precision and Accuracy
A major benefit of Swiss screw machining is its capacity to produce very exact tolerances and excellent surface finishes. The guiding bushing supporting the workpiece extremely near to the cutting tool helps to minimise deflection during the cutting operation. Even in cases where the diameter is small and the item is lengthy and thin, this design greatly improves the accuracy of the machined part.
This degree of accuracy guarantees that every component in large volume manufacturing satisfies precise requirements, therefore minimizing waste, rework, and quality control problems.
2. Perfect for Small and Complex Parts
For creating precise features on complicated pieces, Swiss-type turning is well suitable. CNC Swiss machining can do many operations in one setup—drilling, milling, and tapping—using several axes of motion and live tooling possibilities.
In sectors like medical equipment (e.g., bone screws, surgical tools) that need small components with many functions, this capacity is very valuable.
-
Aerospace components (fasteners, connections, etc.)
-
Electronics—that is, pins and sockets—that <
Swiss lathes handle the component all at once rather than running it through many machines, therefore cutting lead times and handling costs.
3. Excellent High-Volume Run Productivity
Time is money for big volume manufacturing. Running components constantly with no downtime allows Swiss screw machining to provide unparalleled output. Many times fitted with automated bar feeders that enable unattended or “lights-out” operation—that is, the machine may work 24/7 free from continuous monitoring.
For long-term manufacturing runs, Swiss-type turning ideal is achieved by fewer setups, shorter changeover time, and automated component ejection. Over time, manufacturers may create tens of thousands of consistently excellent components, which is very economical.
4. Minimal Secondary Operations
Many times, traditional machining calls for many operations on several machines—cutting on a lathe, then milling, drilling, and finishing elsewhere. Along with adding extra time, this raises the possibility of mistakes.
Many of these auxiliary tasks may be included straight into the machining process using CNC Swiss machining. Without removing the item from the machine, live tooling lets the machine do difficult jobs such cross-drilling and slotting. Time is saved, quality is raised, and labor expenses are lowered by this consolidation.
5. Reduced Resource Waste
In manufacturing, material waste is a major issue particularly with costly metals like titanium, stainless steel, or specialized alloys used in the medical and aerospace industries. < Swiss screw machining reduces waste by means of its effective cutting technique and best use of bar material.
The workpiece is maintained thus near to the tool, which causes less vibration and tool wear, thereby producing more precise cuts and less waste. High volume runs may lead into significant cost reductions here.
6. Flexibility and Scalability
The scalability of Swiss-type turning is one of the main reasons manufacturers use it for. Scaling to hundreds of thousands or maybe millions of units is easy once the software and setup are complete. Modern CNC Swiss machining systems use cutting-edge software that enables simple reprogramming and reconfiguration, therefore facilitating pivot between many component designs or configurations with least downtime.
Fast-moving companies where time-to—-market is critical and product revisions are frequent depend on this adaptability.
7. Capabilities for Automation
Modern production is mostly depending on automation as its pillar. Automation is considered throughout CNC Swiss machining system design. Often including conveyor systems, component catchers, and robotic bar feeders, they let minimum human involvement possible.
Certain sophisticated machines even have built-in sensors to identify tool wear, component variation, or machine faults, therefore guaranteeing constant performance and lowering the need for hand inspections. Swiss machining is perfect for constant, around-the-clock manufacture because of this great degree of automation.
8. Great Return on Investment
Although Swiss-type lathes are more expensive initially than conventional machines, their minimal labor needs, efficiency, and productivity make them a great investment for high- volume applications. A cheaper cost per component results from the shortened cycle durations, less secondary activities, and less downtime.
Manufacturers have a major competitive advantage as over a long production run the cost savings and higher output may far exceed the original expenditure.
In conclusion
Swiss screw machining has unmatched benefits in the field of high-volume precision manufacture. From automated production and scalability to great precision and sophisticated component handling, Swiss-type turning has evolved as the preferred choice for companies looking for great efficiency without sacrificing quality.
Only by combining modern technology with time-tested mechanical design has CNC Swiss machining evolved greater capabilities. Swiss machining provides accuracy, speed, and dependability for sectors where every micron counts and high-volume consistency is essential—making it a crucial component of contemporary production.
Whether you’re manufacturing millions of electronic connections or thousands of surgical screws, Swiss-type turning offers the accuracy, reproducibility, and efficiency large volume manufacturing needs.