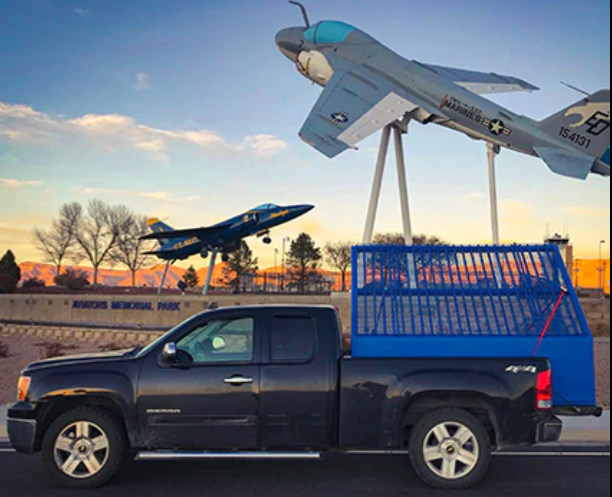
Grizzly screens are vital in the mining, construction, and aggregate industries. They help separate large materials from smaller ones, making processes faster and more efficient. But if you don’t operate them right, you risk costly breakdowns or safety issues. Knowing what mistakes to avoid can save time, money, and even lives.
Understanding the Functionality of a Grizzly Screen
How a Grizzly Screen Works
A grizzly screen uses a series of bars or slats arranged in a grid pattern. These bars filter out large chunks, letting smaller particles fall through. Materials are fed into the top, and the screen separates based on size. It’s like a giant sieve, only tougher and built for heavy-duty use.
Key Components and Their Importance
The main parts include the bars, feed box, drive mechanism, and support frame. The condition of these parts affects how well the screen works. Worn-out bars or loose bolts can slow down operation or cause damage.
Common Mistakes to Avoid When Operating a Grizzly Screen
Overloading the Equipment
Signs of Overloading
When too much material goes in, you might notice longer processing times or the machine vibrating excessively. The feed appears to be too fast, and screens may get clogged.
Consequences of Overloading
Pushing your grizzly screen past its limit can damage the bars and drive system. Over time, this leads to costly repairs and shortens the lifespan of your equipment.
Expert Tips for Proper Load Management
Always stick to manufacturer limits. Keep an eye on how much material you feed in, and adjust for changes in material size or flow. Regularly inspect for blockages or wear.
Failing to Maintain Proper Screen Settings
Importance of Correct Settings
Proper screen setup ensures your material gets separated correctly. If the bars are too far apart or too close, you either lose efficiency or damage your screen.
Common Setup Errors
Incorrectly adjusting the bar spacing or the angle of the screen tilt leads to poor separation or faster wear.
Actionable Maintenance Strategies
Schedule regular checks and calibration. Follow your operation manual, and train staff on proper setup practices. This keeps your machine running smoothly.
Neglecting Routine Maintenance and Inspection
Critical Maintenance Tasks
Look for wear on the bars, check for loose bolts, and lubricate moving parts. Look for cracks or bends that could cause bigger issues.
Impact of Neglecting Maintenance
Skipping check-ups causes unexpected breakdowns. Repairs get more expensive, and safety may become compromised.
Best Practices for Maintenance Schedule
Create a routine checklist. Use diagnostic tools if available. Prevent surprises by fixing issues early.
Operating in Unsafe Conditions
Recognizing Unsafe Environments
Wet or icy conditions increase slip hazards. Poor lighting makes it hard to see problems. Keep the work area stable and clear.
Safety Protocols and Worker Training
Ensure all staff wear proper PPE like helmets and gloves. Post clear safety signs and make sure operators are certified.
Tips for Safe Operation
Monitor weather and work in safer conditions when possible. Train staff on emergency procedures and safe handling practices.
Ignoring Manufacturer Guidelines
Importance of Adhering to Specifications
Following the manual protects your warranty and extends equipment life. It also keeps your operation safe and compliant.
Common Deviations and Their Risks
Modifying parts without advice or using incompatible accessories can cause damage or pose safety threats.
How to Align Operations with Guidelines
Keep staff trained on the latest guidelines. Use only recommended parts and consult manufacturers for support if unsure.
Using the Wrong Accessories or Equipment
Compatibility and Effectiveness of Accessories
Choose screen bars and parts designed for your model. Using the wrong accessories leads to poor performance.
Risks of Improper Use
Incompatible parts can cause breakdowns, reduce throughput, and increase safety hazards.
Tips for Correct Usage
Buy OEM parts, verify compatibility before installation. When in doubt, ask your supplier or manufacturer.
Real-World Case Studies
Some companies faced equipment damage because they overloaded their grizzly screens or ignored maintenance. Once they corrected these mistakes—training staff better and following schedules—they experienced fewer breakdowns and higher productivity. These stories demonstrate the benefits of avoiding costly errors and staying proactive.
Conclusion
Perfecting your use of a grizzly screen begins with avoiding basic mistakes. Stay within load limits, keep settings correct, and follow routine maintenance. Always operate in safe conditions and stick to manufacturer guidelines. By doing this, you will improve your machine’s lifespan, boost productivity, and keep your team safe. Take action now—your equipment and bottom line will thank you.