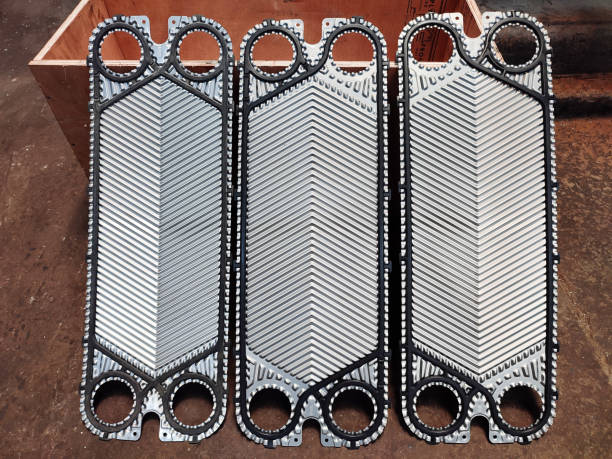
From food processing to chemical manufacture, HVAC systems to pharmaceutical production, plate and frame heat exchanger form a pillar technology in many industrial uses. Their amazing effectiveness in moving thermal energy between fluids without letting them mix has made them invaluable in many fields where exact temperature control is vital. Without appropriate maintenance and cleaning procedures, this efficiency can, however, greatly decline. On heat transfer surfaces, mineral deposits, biological growth, and process pollutants build up over time to create thermal barriers that lower performance, raise energy consumption, and maybe cause expensive system breakdowns. With an eye on inspection techniques, cleaning methods, and preventative maintenance strategies that maximize thermal efficiency and extend equipment life, this thorough book investigates the fundamental practices for preserving and cleaning plate and frame heat exchangers. Understanding these maintenance principles helps industrial operators to guarantee that their heat transfer devices run at maximum performance, therefore reducing downtime and optimizing return on investment in these important thermal management assets.
Knowing Plate and Frame Heat Exchanger Design and Vulnerabilities
A plate and frame heat exchanger’s basic construction is several corrugated plates stacked inside a frame to create alternate channels via which hot and cold fluids pass. These units are far more compact than conventional shell-and- tube substitutes since this arrangement maximizes heat transmission surface area while lowering space needs. Every plate has exactly designed chevron patterns that create turbulent flow conditions, therefore improving thermal transfer efficiency and lowering fouling tendency. While permitting simple disassembly for maintenance, gaskets between plates create sealed paths that stop fluid mixing.
Knowing these design features and natural weaknesses helps one to create efficient maintenance plans that maximize the service life of important heat transfer items and preserve the operational integrity of plate and frame heat exchanger systems.
Creating Workable Monitoring and Inspection Schedules
First line of protection against plate and frame heat exchanger performance degradation is proactive monitoring. By means of a methodical inspection program, operators can identify early warning indicators of fouling, gasket degradation, or mechanical problems before they become system breakdowns. Establishing performance baselines when equipment is clean and running as it should starts effective monitoring from which subsequent data can be matched.
Monitoring temperature all around the heat exchanger offers instant understanding of thermal efficiency. Often indicating fouling development, increasing temperature approach (the difference between output temperatures of the two fluids) suggests decreased heat transfer capability. Another important indicator is the measurement of pressure drop between inlet and exit connectors since fouling reduces flow paths and raises fluid resistance. Rising differential pressure while keeping steady flow rates usually indicates increasing blockage that calls for attention. While these readings complement each other, flow rate monitoring helps to identify partial blockages or poor plate alignment following past repair operations.
By using thorough monitoring systems, operators can maximize maintenance timing—intervening before efficiency losses produce notable energy penalties—while avoiding needless cleaning operations that interrupt production and possibly cause mechanical wear during disassembly and reassembly processes.
Techniques of Chemical Cleaning for Various Fouling Types
Chemical cleaning is a good way to remove deposits without having to completely disassemble the plate and frame heat exchanger units, hence maybe lowering maintenance downtime and related labor costs. But effective application calls for thorough evaluation of fouling type, plate material compatibility, and environmental rules controlling chemical handling and disposal.
Biological fouling calls for several chemical strategies. While specialist enzymatic cleansers target particular biofilm components, oxidizing biocides as sodium hypochlorite or hydrogen peroxide disrupt organic structures and kill microbial colonies. Usually requiring shorter circulation times of 1 to 3 hours, these treatments may be repeated for especially difficult biological accumulations. Following biological cleansing by thorough rinsing stops residual biocide transmission into process streams.
Manufacturers of heat transfer goods provide specialized cleaning solutions designed especially for their equipment, guaranteeing material compatibility with plates, gaskets, and frame components and best performance. Although these unique formulas may have premium cost, their targeted efficacy and lower corrosion risk usually make the expense justified for important process equipment.
Mechanical Cleaning Methods and Disassembly Techniques
Complete disassembly and mechanical cleaning of plate and frame heat exchangers becomes essential when chemical cleaning proves inadequate or fouling has advanced beyond the reach of circulation techniques. This method guarantees appropriate reassembly and allows direct access to heat transfer surfaces but must be carefully executed to avoid damage to delicate components.
The disassembly procedure starts with thorough documentation of the current plate layout, including pictures and dimension measurement of the compacted plate pack. Especially for exchangers with several plate configurations or various corrugation patterns, this reference material becomes quite helpful during reassembly. Once operators separate individual plates, preserving their sequence and alignment to keep the intended flow pattern, they can remove tightening bolts progressively and evenly to prevent frame distortion.
Techniques of plate cleaning must strike a compromise between the risk of destroying the thin metal surfaces and their crucial corrugation patterns against deposit removal efficacy. Applied at the correct angle and distance from plate surfaces, high-pressure water jetting (usually 500–1000 psi) effectively cleans for mild deposits. Soft-bristle brushes with compatible cleaning solutions provide mechanical agitation without harming plate surfaces for more persistent accumulations. As they destroy protective passivation layers and cause microscopic damage that speeds future fouling attachment, abrasive equipment including wire brushes, metal scrapers, or sandblasting must never come into touch with plate surfaces.
Professional service providers provide complete mechanical cleaning programs especially for plate and frame heat exchangers for companies without specialized maintenance experience. Often justifying their cost by lower downtime and longer equipment life, these experts provide purpose-designed cleaning tools, suitable safety procedures, and great experience that lowers the chance of harm during maintenance activities.
Strategic Preventive Maintenance and Performance Enhancement
Using thorough preventive maintenance plans greatly increases plate and frame heat exchanger service life beyond reactive cleaning, hence enhancing thermal performance between cleaning cycles. By addressing core causes of fouling formation and mechanical degradation, these proactive strategies lower maintenance frequency and increase operational dependability of these fundamental heat transfer devices.
Many applications’ basis for fouling prevention is water treatment programs. While correct pH reduces corrosion potential, softening or chemical sequestration helps to control water hardness, thereby preventing scale development. Before they reach heat exchanger channels, filtration systems remove suspended particles, therefore tackling particulate fouling at its source. Well-run biocide programs stop biological growth in cooling water applications by using alternating treatment chemicals that stop resistant organism development.
In non-water applications, process stream pretreatment similarly addresses fouling tendencies. Strata or filters installed upstream of plate and frame heat exchangers catch particles before they come to heat transfer surfaces. In chemical processing uses, strategies for temperature management that keep process fluids below precipitation thresholds stop crystallization fouling. Frequent process stream laboratory examination helps determine changing fouling potential prior to effects on exchanger performance.
Completing the preventative maintenance ecosystem are predictive analysis and documentation. Keeping thorough service records helps one to see performance patterns and deterioration rates, hence enabling adjustment of cleaning intervals depending on real system behavior instead of general suggestions. Heat exchanger monitoring integrated into computerized maintenance management systems allows condition-based maintenance scheduling that best uses resources and reduces manufacturing interruptions.
Oversaw Specialized Maintenance for Important Projects
Because of special cleanliness standards, dangerous process fluids, or crucial operational needs, several sectors provide particular difficulties for plate and frame heat exchanger maintenance. These specialized uses call for customized maintenance strategies that balance application-specific limitations against cleaning efficacy, therefore guaranteeing dependability of these essential heat transfer items.
Different difficulties arise in chemical processing involving caustic, poisonous, or reactive compounds. When servicing exchangers exposed to hazardous pollutants, maintenance staff need specific training and the proper personal protection gear. Usually needing several flushing cycles with neutralizing agents and verification testing before disassembly, decontamination processes must come first in relation to maintenance activities. In these uses, the choice of plate and gasket material becomes very important since inappropriate compatibility might hasten degradation and generate safety concerns during maintenance activities.
Conclusion
Organizations trying to improve equipment life, reduce energy consumption, and guarantee dependable thermal management across industrial processes must first maintain and clean plate and frame heat exchangers. The multifarious approach covered in this guide—including monitoring systems, chemical and mechanical cleaning techniques, preventive methods, and unique application concerns—offers a whole framework for maximizing these important heat transfer products. Industrial operators can avoid both early equipment failure and too aggressive cleaning interventions by using suitable maintenance techniques customized to particular operating conditions and fouling difficulties, therefore attaining the right balance between maintenance expense and performance gain. Through lower energy consumption and resource use, regular inspection, timely cleaning, and planned performance optimization not only increase equipment service life but also greatly help with sustainability objectives. At Kinetic Engineering Corporation, we stress thorough maintenance support alongside creative exchanger designs since we know that properly maintained plate and frame heat exchangers offer exceptional value throughout their operational lifetime, so enabling our customers to achieve the lowest total cost of ownership for these indispensable thermal management systems while meeting demanding performance requirements across many industrial applications.