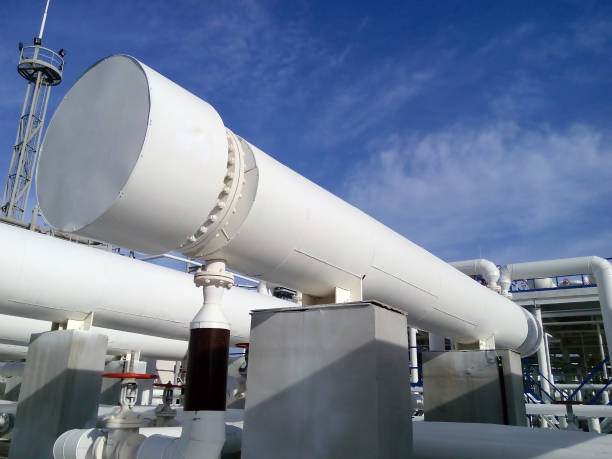
In process engineering design, choosing the suitable heat transfer equipment for industrial uses is among the most important choices made. Effective thermal management systems catered to particular process needs define the efficiency, dependability, and financial viability of many industrial activities. Heat transfer equipment is the essential infrastructure allowing controlled heating, cooling, and temperature maintenance from chemical processing and power generation to food production and HVAC systems. The variety of heat transfer products on the market reflects the range of industrial requirements; each technique has unique benefits for a given use. Among these, the shell and tube heat exchanger is one of the most widely used solutions due to its durability, high heat transfer efficiency, and adaptability to high-pressure and high-temperature applications. Making a wise choice calls for a thorough awareness of process parameters, performance traits of several technologies, material compatibility issues, geographical restrictions, and lifetime cost consequences. Examining the important elements that should affect your decision-making process, this article offers a methodical way to assess and choose heat transfer equipment. Methodically evaluating your particular needs and knowing the advantages and drawbacks of various heat transfer methods, including the shell and tube heat exchanger, can help you to choose the best option that strikes performance, dependability, efficiency, and economy for your particular use.
Recognizing Your Heat Transfer Needs
Analyzing your process needs and operational conditions is crucial before assessing particular forms of heat transfer equipment. This basic evaluation guarantees that the chosen equipment will satisfy performance criteria and operate consistently inside your process environment, therefore defining the limits against which possible solutions can be tested.
Selection of equipment starts with process fluid properties. Direct influence of the physical and chemical characteristics of the hot and cold streams—including viscosity, specific heat capacity, thermal conductivity, density, and phase change behavior—directly affects heat transfer mechanisms and equipment fitability. Particularly viscous fluids could call for specific designs to guarantee sufficient flow distribution and reduce fouling possibilities. Corrosive or hazardous fluids call for cautious material selection and may favor some equipment types that reduce leak potential or enable inspection and maintenance.
The basic performance standards are set by thermal duty requirements. Usually stated in kilowatts or BTU/hr, the necessary heat transfer rate defines the equipment capacity. The mean temperature difference driving heat transfer and influence equipment type selection is found by temperature profiles for both streams including target and inlet outlet temperatures. The latent heat requirements for applications involving phase change—condensation or evaporation—must be precisely computed since these processes usually control the total thermal demand.
Operating pressure and temperature ranges mechanically limit equipment design. While extreme temperatures limit material alternatives and may call for specific construction approaches, high-pressure applications may prefer sturdy shell-and- tube exchangers over plate designs. Equipment choice also depends on pressure differential between streams since some designs more successfully manage significant pressure variations between streams than others.
Particularly in retrofit projects or facilities with restricted real estate, space and weight restrictions sometimes become deciding elements. While shell-and- tube systems might be favored where vertical space is available but horizontal space is constrained, compact heat transfer equipment such as plate heat exchangers may have advantages where footprint minimization is required. Additionally taken into account is installation location accessibility for maintenance; some heat transfer solutions demand large clearance for tube bundle removal or plate access.
Budget concerns cover lifetimes as well as original capital expenses. Although purchase price is easily known, the total cost of ownership should incorporate installation, energy use, maintenance needs, estimated service life, and possible manufacturing effects during maintenance downtime. Through lower energy costs and improved process performance, high-efficiency designs may charge premium prices but provide excellent return on investment.
Heat Transfer Equipment Types and Uses
There are many heat transfer equipment choices available on the industrial market, each meant to shine under particular running conditions. Knowing the basic features, benefits, and constraints of every technology helps one to choose the right one for a given use.
Particularly for liquid-liquid and condensing uses, shell and tube heat exchangers are the most often used heat transfer devices in process industries. While several internal configurations (fixed tubesheet, floating head, U-tube) address distinct thermal expansion and maintenance requirements, their strong structure manages high pressures and temperatures. Standardizing designs for various services, TEMA (Tubular Exchanger Manufacturers Association) classes help to ease specification. Applications needing vast heat transfer surfaces or accommodating high pressure differentials between fluid streams call for these exchangers most especially. Among the common uses are steam generators, condensers, reboilers, and oil coolers. Among the limitations include quite big footprints, additional weight, and more difficult cleaning techniques for severely fouling applications.
Excellent thermal efficiency in small sizes makes plate heat exchangers highly sought-after in many different sectors. Their corrugated plates reduce fouling tendencies and produce turbulent flow patterns that improve heat transfer coefficients. While brazed plate versions provide more compact construction at the cost of maintenance accessibility, gasketed plate designs provide simple disassembly for inspection and cleaning. Applications with near temperature approaches, limited space, or regular cleaning needs call for these units most especially. These heat transfer products are used often in food and beverage processing, HVAC systems, and pharmaceutical activities. Constraints on pressure and temperature brought on by gasket materials and the possibility for expensive gasket replacement in some uses define limitations.
In water-starved areas or where cooling water quality is problematic, air-cooled heat exchangers are quite important since they offer cooling without water consumption. Through finned tube bundles with forced or induced draft air flow, these machines directly reject heat straight to the atmosphere. Variable speed fans and automatic louver systems are included into modern designs to preserve exact temperature regulation and maximize energy use under different ambient circumstances. Typical uses are remote site process fluid cooling, compressor intercooling, and gas cooling. Among the limitations are possible noise issues in populated locations, susceptibility to ambient temperatures, and footprints more than those of water-cooled substitutes.
For problematic fluids with strong fouling tendencies or including suspended particulates, spiral heat exchangers have special benefits. Excellent heat transfer efficiency and high velocities maintained by its single-channel, counter-current flow design produce self-cleaning effects. More successfully than many alternatives, these devices manage slurries, viscous materials, and particulate-laden streams. Spiral exchangers are used routinely in wastewater treatment, pulp and paper production, and chemical recovery processes. Higher manufacturing costs and more difficult mechanical cleaning techniques when necessary constitute limitations.
For uses requiring extraordinary simplicity, pressure capability, and thermal efficiency, printed circuit heat exchangers offer state-of-the-art technology. These units diffuse-bonded into a solid block from fluid channels chemically etched into metal plates. With outstanding heat transfer performance, the resulting equipment manages severe pressures (up to 600 bar) and temperatures. These specialized heat transfer materials are used extensively in cryogenic gas processing, offshore oil and gas applications, and supercritical CO2 systems. Higher capital costs, limited capacity to support fouling services, and specialized manufacturing needs are among the limitations.
Materials for Maximum Longevity and Performance
Performance, dependability, longevity, and cost of heat transfer equipment are strongly influenced by the construction materials. By choosing suitable materials depending on fluid properties and process conditions, one can maximize thermal efficiency and economic value while preventing early failures.
For non-corrosive applications running within reasonable temperature ranges, carbon steel is still the most affordable choice. For many water, steam, and hydrocarbon applications, its good mechanical characteristics, fabricability, and thermal conductivity fit Appropriate corrosion allowances or internal coatings/linings usually help to explain increased lifetime. The main constraints are unsuitability for many chemical processing uses and low resistance to water corrosion without protection.
For many uses, stainless steels have exceptional corrosion resistance. Particularly in oxidizing conditions, Austenitic grades (304/304L, 316/316L) offer good overall corrosion resistance while preserving suitable heat conductivity. More demanding services call for duplex stainless steels since they offer improved strength and stress corrosion cracking resistance over austenitic grades. Food and beverage processing, pharmaceutical uses, and chemical processing all find extensive application for these alloys. Higher cost than carbon steel and sensitivity to particular corrosion mechanisms under some circumstances are among the drawbacks.
Non-ferrous alloys meet needs outside of those of stainless steel. Common in HVAC uses and power plant condensers, copper and copper alloys offer outstanding heat conductivity and exceptional corrosion resistance in non-oxidizing settings. Strong acids and high-temperature oxidizing environments are among the very corrosive situations nickel alloys resist. Though at premium price, titanium provides exceptional seawater corrosion resistance with a strong strength-to—-weight ratio. Every material has different manufacturing concerns and galvanic compatibility problems that have to be taken into account during choice.
Specialty materials solve extremely demanding niche applications. While glass-lined equipment finds ultra-pure uses where metal ion contamination must be avoided, graphite heat exchangers handle highly corrosive substances that attack metallic components. For some harsh chemical applications, fluoropolymer-lined heat transfer equipment combines cost with corrosion resistance. Beyond metallic capabilities, ceramic heat exchangers resist severe temperatures and hostile chemical conditions.
Along with the main process fluids, material choice must take into account cleaning agents, sporadic process upsets, startup/shutdown circumstances, and possible pollutants. Particularly in heat transfer equipment where temperature gradients, fissures, and flow disturbances provide circumstances favoring pitting, crevice corrosion, or stress corrosion cracking, localized corrosion mechanisms sometimes prove more troublesome than general corrosion. By consulting material experts, industry knowledge, and corrosion data, one can help to prevent unanticipated downtime and expensive failures during the choosing process.
Performance Optimizing and Efficiency Issues
Directly affecting running costs and environmental impact is thermal efficiency. Modern heat transfer systems minimize energy usage and running costs while nevertheless providing many features and choices to maximize performance for particular uses.
By use of changed surface geometries, heat transfer improvement methods greatly increase efficiency. Improved tubes with interior ridges, dimples, or spiral patterns encourage turbulence upsetting boundary layers and raising heat transfer coefficients. Corrugated patterns used in plate heat exchangers produce intricate flow channels with outstanding mixing properties. These improvements enable more compact equipment designs that lower material requirements and space needs while providing either equivalent or better thermal performance over traditional surfaces.
Optimizing flow arrangement maximizes the driving temperature difference all around the apparatus. The most effective use of the given temperature differential is made via counter-current flow configurations in which hot and cold streams move in opposing directions. Even within general cross-flow setups, multi-pass designs produce local counter-current flow patterns. In shell-and- tube exchangers as well as in flow distribution in plate units, proper baffle design guarantees consistent velocity profiles that avoid dead zones and channeling.
Features meant to reduce fouling over time maintain performance. While smooth surfaces minimize adhesion sites for possible foulants, self-cleaning systems preserve high fluid velocities that prevent deposit buildup. Equipment layouts that support frequent inspections and cleaning help to reduce efficiency loss during maintenance intervals. Selecting heat transfer equipment with adequate fouling factors and cleaning access is absolutely essential for applications with known fouling tendencies to maximize lifetime performance.
Opportunities for energy recovery go beyond personal device choice to system-level issues. Pinch analysis methods find ideal locations for heat transfer equipment within process streams to enhance energy recovery and reduce outside heating and cooling needs. By capturing thermal energy normally wasted to the environment, waste heat recovery systems increase general facility efficiency. Low-temperature waste heat is upgraded by heat pump technologies to reach desired temperature levels, therefore allowing innovative energy integration solutions.
Integration of control systems guarantees best performance in many different environments. Sensors and control interfaces included in modern heat transfer systems help to provide real-time performance monitoring and adjustment. Intelligent controls, automatic venting systems, and variable flow capabilities keep peak efficiency independent of changing process demand or ambient circumstances. These sophisticated capabilities lower operator intervention needs while nevertheless providing exceptional performance.
Installation, Maintenance, and Lifespans
Without correct installation, operation, and maintenance, even the most well chosen heat transfer equipment will underperform. Creating thorough lifecycle management plans guarantees consistent performance, reduces unnecessary downtime, and maximizes return on investment.
Long-term performance is largely influenced by installability factors. While good piping design avoids strain on nozzles and connections, proper foundation design fits equipment weight and thermal expansion forces. Facility layouts have to include enough clearance for maintenance operations, especially for equipment needing plate access or bundle removal. With temperature and pressure measuring stations at strategic sites, instrumentation installation should support performance monitoring and troubleshooting. Expert installation done according to manufacturer recommendations helps to avoid numerous typical issues compromising dependability and efficiency.
Commissioning processes check correct operation and set baseline performance criteria. Complete cleaning of connected piping systems helps to avoid debris introduction that can lead to fouling or damage. Good venting releases trapped air that might otherwise hinder heat transfer. Performance testing in real-world running conditions guarantees that the equipment satisfies design criteria and provides reference data for next evaluation. For maintenance staff, thorough documentation of installation and commissioning offers priceless reference information.
Programs for preventative maintenance help to extend service life and retain performance. Not just calendar time, but also regular inspection schedules depending on operating conditions enable quick intervention before major performance degradation takes place. Key parameter monitoring—including approach temperatures, pressure declines, and general heat transfer coefficients—allows early warning of impending problems. While gasket and seal inspection stops unexpected leakage, cleaning techniques catered to particular fouling mechanisms preserve thermal efficiency. In shell-and- tube systems, tube integrity testing points up possible breakdowns before they start.
To maximize overall ownership costs, lifetime cost management combines initial capital investment with continuous operating and maintenance expenses. Through longer service life, lower maintenance needs, or better energy economy, more initial investment in premium materials or advanced designs often yields outstanding return. Enhanced surface technologies or control system modifications are among retrofit options that can rejuvenate current heat transfer equipment to satisfy changing process needs or efficiency goals. Replacement strategies based on equipment condition and performance trends help to maximize capital use by preventing disruptive emergency failures.
Training courses guarantee operators and maintenance staff know correct techniques for the particular heat transfer devices used in their plants. Through better operational methods, quick diagnosis of developing problems, and correct application of maintenance actions, this knowledge investment pays off. Technical documentation, troubleshooting instructions, and expert consultation among other manufacturer support tools offer great help all through the equipment life.
Modern Technologies and Next Developments
Heat transfer equipment’s sector is always changing and many developments show improved performance, less environmental effect, and more applications possibilities. Maintaining knowledge of these changes enables facility managers and engineers to make forward-looking decisions that best position their operations for future needs.
By allowing intricate geometries impossible to create with traditional manufacturing techniques, additive manufacturing—3D printing—technology is transforming heat exchanger design. These cutting-edge manufacturing processes produce integrated features, ideal flow pathways, and until impossible surface improvements. Although right now concentrated on specific uses, as costs drop and capacities grow these production techniques are progressively finding their place in more general market categories.
Embedded sensors, wireless connectivity, and sophisticated analytics tools included in smart heat exchangers turn conventional machinery into intelligent assets. These technologies allow predictive maintenance based on actual condition instead of set intervals, real-time performance monitoring, and automatic adjustment to changing conditions. Integration with asset management systems and facility-wide digital twins offers complete view over whole thermal systems.
Emerging heat transfer media with better characteristics are phase change materials and nanofluids. While designed nanofluids have thermal conductivities much higher than traditional heat transfer mediums, microencapsulated phase transition materials stabilize temperatures by latent heat effects. Although commercialization still presents difficulties with long-term stability and economic feasibility, these specialty fluids allow more compact equipment designs or higher performance inside current space limits.
Innovations with sustainability emphasis help to solve environmental issues. Selection parameters like low global warming potential refrigerants, better water consumption designs, and materials with lower embodied carbon are growingly significant. Low-temperature differentials typical of geothermal sources or solar thermal applications as well as other renewable energy integration-oriented heat transfer technologies help more general energy transition projects. Many times, these ecologically friendly solutions provide operational advantages along with regulatory compliance benefits.
While increasing quality control, modular and prefabricated systems simplify installation. Pre-engineered components found in factory-assembled modules provide quicker installation times, less on-site work needed, and more consistent performance. Remote locations, fast-track projects, or applications needing specialist knowledge not easily accessible at installation sites benefit especially from these methods.
Conclusion
Choosing ideal heat transfer equipment means juggling many technical, operational, and financial aspects to find solutions that provide exceptional performance, dependability, and value all through their lifetime. Starting with careful examination of your particular needs—including thermal duty, fluid qualities, operational conditions, and geographical constraints—which lays the groundwork for good decision-making, the process starts Knowing the relative benefits and drawbacks of various heat transfer technologies helps you to reduce the choice to equipment kinds best fit for your use. While efficiency improvement characteristics maximize continuous operational costs, material selection depending on compatibility with process fluids and operating circumstances guarantees lifetime and dependability. Good lifespan economics depend much on proper installation, commissioning, and maintenance techniques preserving performance and extending equipment life. Maintaining knowledge about new possibilities and future trends helps your business to be positioned favorably for changing needs and opportunities as technology keep developing. Applying the method described in this article will help you to boldly choose heat transfer equipment that satisfies immediate process needs and provides long-term value. Kinetic Engineering Corporation provides complete consultation services and advanced heat transfer products customized to your particular needs for complicated applications needing specialized knowledge or custom-engineered solutions, so guaranteeing optimal performance and dependability for your most demanding thermal management problems.