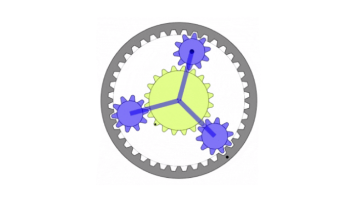
When engineers talk about precision, durability, and compact motion systems, the cycloidal gearbox often remains an underrated yet powerful solution. As automation and robotics evolve, demand is growing for transmission systems that combine high torque capacity with minimal backlash, compact form, and extended lifespan. Enter the cycloidal gearbox—an innovation that’s changing how industries approach mechanical efficiency.
In this article, we’ll explore what makes the cycloidal gearbox unique, how it works, where it’s used, and why it’s rapidly gaining attention in modern mechanical design.
What Is a Cycloidal Gearbox?
At its core, a cycloidal gearbox is a type of speed reducer that operates based on the cycloidal motion principle. Unlike traditional gearboxes that rely on involute gears, cycloidal drives use a disc that rolls along a set of pins in a cycloidal path. This motion allows torque transmission with significantly reduced stress and wear on the components.
The gearbox comprises three main components:
-
High-speed input shaft with an eccentric cam
-
Cycloidal disc that follows the cam’s movement
-
Output pins or rollers arranged in a circular pattern
When the input shaft rotates, it drives the cycloidal disc in a unique wobbling motion. This motion, in turn, pushes the output pins, producing a smooth and controlled rotation at the output shaft—typically at a much slower speed and higher torque.
What Makes Cycloidal Gearboxes Stand Out?
There are several reasons why design engineers are turning to cycloidal gearboxes for challenging mechanical applications:
1. High Torque Density
Cycloidal gearboxes can handle loads that would be problematic for similarly sized planetary or spur gear reducers. Thanks to the multiple contact points between the cycloidal disc and output pins, the torque is distributed evenly across the system.
2. Minimal Backlash
Backlash—slack or lost motion in a mechanism—can severely reduce positioning accuracy. Cycloidal gearboxes are inherently low-backlash due to their preloaded rolling contact design, making them ideal for robotics, CNC machinery, and precision automation.
3. Exceptional Durability
The rolling action within a cycloidal gearbox results in minimal friction and wear. Unlike traditional gear teeth that experience concentrated stress, cycloidal discs spread the load over several contact points. This not only enhances lifespan but also reduces maintenance costs.
4. Shock Load Resistance
Cycloidal gearboxes excel in applications with fluctuating loads or sudden impacts. Their robust construction allows them to absorb up to 500% of their rated torque for short durations, making them excellent for heavy-duty industrial tasks.
Key Applications of Cycloidal Gearboxes
Due to their distinctive advantages, cycloidal gearboxes are being adopted across various sectors:
Robotics and Automation
Precision motion, compact size, and low backlash make cycloidal drives a natural fit in robotic arms and industrial automation systems. They help achieve smooth, precise movements even in complex, multi-axis systems.
Machine Tools and CNC Equipment
Cycloidal gearboxes enable ultra-precise positioning and motion control in CNC lathes, mills, and grinding machines, where tolerances can be as tight as a few microns.
Packaging and Food Processing
The smooth motion and high reliability of cycloidal gearboxes are essential in applications requiring hygiene, consistency, and speed, such as automated packaging lines and food processing equipment.
Conveyors and Material Handling
Cycloidal gear drives power many conveyor systems due to their ability to handle heavy loads, resist shock, and maintain consistent output speed.
Cycloidal Gearbox vs. Planetary Gearbox
While both types of gearboxes are used for reducing speed and increasing torque, the cycloidal gearbox edges ahead in several areas:
Feature | Cycloidal Gearbox | Planetary Gearbox |
---|---|---|
Backlash | Very low | Moderate to low |
Torque Capacity | High for size | Moderate to high |
Shock Load Tolerance | Excellent (up to 500%) | Limited |
Noise and Vibration | Low | Moderate |
Service Life | Long (minimal wear) | Good, but component wear possible |
If your application demands high accuracy, minimal backlash, and long-term durability, the cycloidal gearbox often becomes the superior choice.
Design Considerations
Before selecting a cycloidal gearbox, it’s crucial to evaluate the specific application parameters:
-
Load Type: Is it dynamic or static? Continuous or intermittent?
-
Input Speed: Cycloidal gearboxes are well-suited for moderate-speed input applications.
-
Torque Requirements: Ensure the gearbox can handle peak and nominal torque loads.
-
Size Constraints: While compact, cycloidal gearboxes may require customized mounting depending on your design.
Working with a reputable gearbox supplier or design partner ensures you select the most appropriate configuration for your application, from horizontal to vertical layouts and dual-shaft options.
Future of Cycloidal Gearboxes in Industry 4.0
As smart manufacturing continues to evolve, the demand for more accurate, efficient, and maintenance-free systems is growing. Cycloidal gearboxes fit perfectly into this vision, providing high-performance mechanical solutions that pair seamlessly with modern digital controls, sensors, and feedback systems.
Innovations in materials (e.g., hardened alloys, composites), lubrication, and integration with servo motors are pushing cycloidal technology even further, making it a future-proof choice for next-gen industrial systems.
Final Thoughts
The cycloidal gearbox may not have the name recognition of some other gearbox types, but in many high-performance applications, it’s the unsung hero delivering power, precision, and reliability where it counts. As industries prioritize efficiency and compact design, this innovative gearbox is poised to become a mainstay in mechanical engineering.