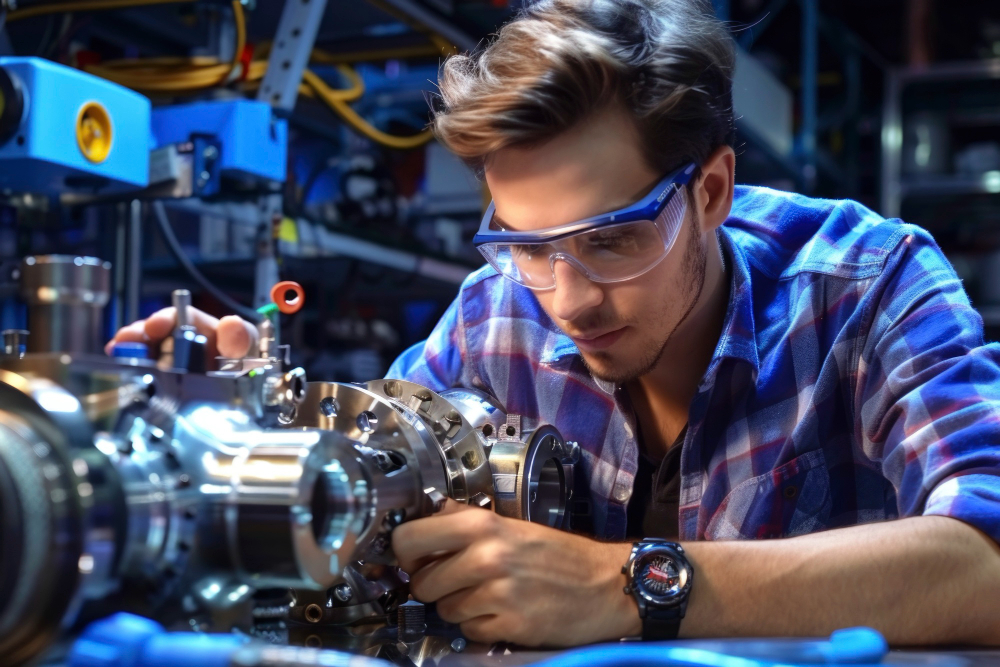
In any system involving rotating shafts—whether in pumps, compressors, or mixers—preventing leaks where the shaft enters a sealed housing is critical. That’s where mechanical seals come in. These compact but powerful components are designed to prevent fluid leakage, reduce friction, and extend equipment life, making them vital in a wide range of industries, from marine and oil & gas to water treatment and food processing.
In this blog, we’ll explore what mechanical seals are, how they work, their types, and why they are preferred over traditional sealing methods like gland packing.
What is a Mechanical Seal?
A mechanical seal is a device used to contain fluid within a rotating piece of equipment—such as a pump or mixer—by preventing it from leaking out along the shaft. It does this by creating a seal between the rotating shaft and the stationary pump housing.
Unlike older sealing methods that rely on compression packing (which requires constant tightening and causes shaft wear), mechanical seals are more efficient, reliable, and easier to maintain.
How Does a Mechanical Seal Work?
A typical mechanical seal consists of two main components:
-
Rotating face (seal ring): Attached to the shaft, it rotates with it.
-
Stationary face (mating ring): Fixed to the pump casing.
These two faces are pressed together with a spring or bellows, creating a very flat interface. A thin film of fluid between them provides lubrication and prevents dry running, but is thin enough to restrict leakage. The key is that the seal faces must be precisely machined and kept clean to avoid wear and failure.
Supporting Components Include:
-
Secondary seals (O-rings or gaskets)
-
Spring or bellows assembly (to maintain pressure)
-
Retaining hardware (collars, set screws, glands)
Types of Mechanical Seals
Mechanical seals are classified based on design and application. Common types include:
1. Balanced vs. Unbalanced Seals
-
Balanced seals are used for high-pressure systems and reduce face loading, resulting in less wear.
-
Unbalanced seals are suitable for lower pressures and are simpler in design.
2. Single vs. Double Seals
-
Single seals use one set of sealing faces and are common in clean, low-risk applications.
-
Double seals (tandem or back-to-back) are used in hazardous or high-pressure systems, offering extra protection.
3. Cartridge Seals
-
Pre-assembled for easy installation and maintenance.
-
Minimize installation errors and are commonly used in modern equipment.
4. Pusher vs. Non-Pusher Seals
-
Pusher seals use dynamic O-rings and springs.
-
Non-pusher seals use bellows, ideal for high-temperature or clogging-prone fluids.
Advantages of Mechanical Seals
Leak Prevention: Far superior sealing than gland packing, reducing environmental and safety risks.
Extended Equipment Life: Less shaft wear and friction lead to longer pump life.
Lower Maintenance: Requires less frequent adjustment and servicing.
Energy Efficiency: Reduced friction means lower power consumption.
Cleaner Operation: Essential in sanitary or hazardous applications where leaks can’t be tolerated.
Applications of Mechanical Seals
Mechanical seals are used in a broad range of sectors:
-
Marine: Pumps, compressors, and seawater systems
-
Industrial: Chemical, oil & gas, pharmaceutical, and food processing industries
-
Water Treatment: Pumps for potable and wastewater systems
-
HVAC: Chiller and cooling system pumps
-
Power Generation: Circulating and feedwater pumps in thermal plants
Maintenance and Best Practices
To ensure long service life and optimal performance:
-
Keep seal faces clean during installation
-
Avoid dry running the pump
-
Use proper seal flush plans to remove heat and debris
-
Monitor for vibration, pressure surges, and fluid contamination
-
Replace worn secondary seals during overhauls
Conclusion
Mechanical seals may seem like a small part of a complex system, but they play a crucial role in maintaining operational efficiency, safety, and environmental compliance. By understanding their function, types, and maintenance needs, you can ensure longer equipment life, fewer leaks, and more reliable performance in any application.
Whether you’re maintaining a marine engine room or managing a chemical plant, investing in the right mechanical seal and maintaining it properly is a smart, cost-effective decision.